What is Micro Dispensing? Everything You Need to Know
11/19/20248 min read
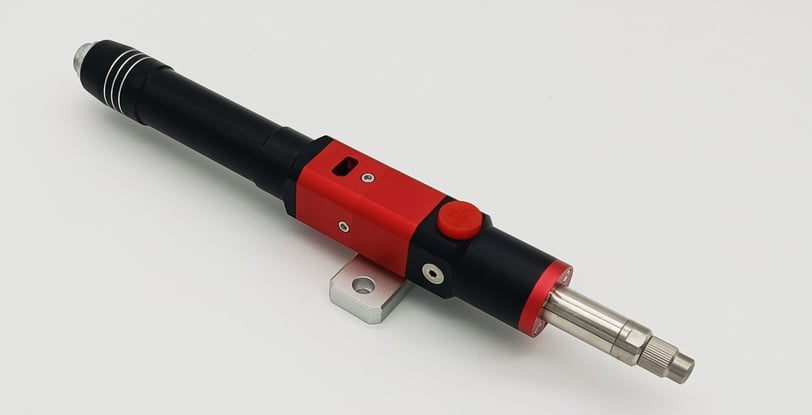
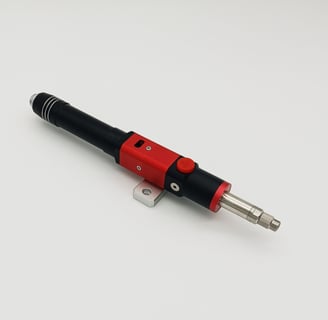
Understanding Micro Dispensing Technology
Micro dispensing technology refers to the precise delivery of small volumes of fluids, often in the microliter or nanoliter range. This innovative method has gained recognition across various industries, including pharmaceuticals, electronics, and food production, primarily due to its ability to manage fluids with unparalleled accuracy. At its core, micro dispensing is engineered to eliminate the inefficiencies associated with traditional dispensing methods, such as pouring or even larger-scale syringe dispensing. The advantages of micro dispensing come from its ability to minimize waste while enhancing control over fluid characteristics.
The history of micro dispensing can be traced back to advancements in science and technology pushing the boundaries of what is possible in fluid management. Early experiments laid the groundwork for modern tools, enriching applications such as analytical chemistry, where precision is of utmost importance. Over time, innovations have led to the development of specialized devices designed for micro dispensing, such as piezoelectric dispensers and non-contact dispensing systems. These devices utilize various mechanisms to deliver incredibly accurate amounts of liquid, including pressure injection and ultrasonic vibrational methods.
In contrast to traditional dispensing techniques, micro dispensing offers substantial improvements in precision and repeatability. Conventional methods can struggle with the variability often associated with handling small volumes; however, micro dispensing aims to mitigate this by implementing advanced technologies and sophisticated algorithms to ensure consistent results. Moreover, the objectives of micro dispensing focus on not just accuracy but also scalability and versatility, allowing it to adapt across diverse applications. Nevertheless, significant challenges remain in the pursuit of perfecting micro dispensing technology, including the need for compatibility with a range of fluids and ensuring reliability in various environmental conditions. These dynamics make micro dispensing a rapidly evolving field, central to advancements in multiple industries.
Types of Micro Dispensing Systems
Micro dispensing systems have gained popularity across various industries due to their precision and efficiency in dispensing small volumes of liquids and adhesives. These systems come in multiple types, each designed to serve specific operational needs and applications. The primary categories include piezoelectric, pneumatic, and mechanical dispensers.
Piezoelectric dispensers utilize a piezoelectric element to control the dispensing of fluids. When an electrical voltage is applied, the element deforms, creating a pressure pulse that expels a precisely measured amount of liquid. This type of system is known for its accuracy and ability to handle low-viscosity fluids, making it ideal for applications in the electronics and medical sectors, where exact dosages are crucial.
Pneumatic dispensers, on the other hand, operate by using compressed air to create a pressure differential that drives the fluid out of the dispensing nozzle. These systems are well-suited for viscous fluids and are commonly employed in industries such as automotive and packaging. Pneumatic systems can be designed for various operational modes, including continuous flow and timed pulse dispensing, providing versatility depending on the user's requirements.
Mechanical dispensers consist of moving parts, such as pumps or valves, that physically push or draw liquids into the dispensing chamber before ejecting them through a nozzle. This type of dispenser is robust and can handle a wide range of fluid viscosities and properties. Mechanical systems are frequently used in food processing and cosmetics, where larger quantities of substances may need dispensing. Additionally, their ability to dispense a variety of materials, including those containing particulates, makes them an excellent choice for diverse applications.
In conclusion, selecting the right micro dispensing system depends significantly on the specific requirements of the application, including the type of fluid, viscosity, and accuracy needed. Understanding the functionalities of each type can help in making informed decisions to meet operational goals effectively.
Applications of Micro Dispensing
Micro dispensing technology has emerged as a pivotal solution across various industries, significantly enhancing processes and addressing unique challenges. In the medical sector, micro dispensing is crucial for precision in drug delivery systems. For example, it is employed in creating micro pumps that administer minute doses of insulin or other medications, ensuring optimal therapeutic outcomes while minimizing side effects. This level of accuracy is crucial in enhancing patient care and improving adherence to treatment protocols.
In the electronics industry, micro dispensing plays a vital role in the assembly of electronic components. It is frequently utilized in the application of adhesives or solder pastes in a controlled manner. This micro application not only reduces material waste but also enhances the reliability of electronic devices by ensuring consistent coverage and bonding strength on intricate components. Such a method allows manufacturers to produce compact designs essential for modern technology.
The pharmaceutical industry benefits greatly from micro dispensing by enabling the formulation of drugs in novel ways. Specifically, it is used to create highly concentrated formulations that may involve complex mixtures, such as suspensions or emulsions. These formulations necessitate precision to achieve consistent product quality, and micro dispensing technology provides the required control over the dosing processes. Moreover, the ability to dispense micro amounts facilitates the development of personalized medicine, where therapies can be tailored to individual patient needs.
Research institutions also leverage micro dispensing for various applications, such as the creation of microarrays in biological studies. Here, micro dispensing allows researchers to apply small, defined volumes of reagents, enabling high-throughput screening and accurate experimental results. Overall, the implementation of micro dispensing technology is revolutionizing these fields, driving innovation and enhancing operational efficiency.
Benefits of Micro Dispensing Technology
Micro dispensing technology serves as a cornerstone for numerous industries, providing a plethora of advantages that facilitate improved operational efficiency and product quality. One of the most significant benefits is the enhanced precision it offers. By utilizing advanced micro dispensing systems, manufacturers can dispense tiny amounts of liquids or materials with remarkable accuracy. This precision reduces the margin for error, ensuring that each application meets stringent quality standards.
Moreover, micro dispensing technology significantly contributes to reducing waste. Traditional dispensing methods often result in excess material being dispensed or misapplied, leading to increased costs and environmental concerns. With micro dispensing, processes are optimized to minimize wastage by delivering only the necessary amount of material, promoting sustainability along the way. This characteristic makes it particularly appealing in sectors where resource conservation is critical.
In terms of process efficiency, micro dispensing technology enables faster production cycles. The quick and accurate delivery of materials not only accelerates the manufacturing process but also allows for greater flexibility in production lines. This adaptability is vital in industries such as electronics, pharmaceuticals, and biotechnology, where rapid response to market demands is essential.
Scalability is another notable benefit of micro dispensing systems. As businesses grow and their production needs evolve, micro dispensing technologies can be easily adjusted to accommodate larger scales without compromising quality. This adaptability ensures that companies can remain competitive as they expand their operations.
Lastly, micro dispensing contributes to cost savings by enhancing product quality and reducing material costs. The precision and efficiency of these systems result in fewer defects and less rework, ultimately leading to higher customer satisfaction and loyalty. As organizations move towards implementing micro dispensing technologies, they can expect not just economic benefits but also an uplift in overall product performance.
Advancements in Micro Dispensing Systems
Micro dispensing technology has seen significant advancements in recent years, propelling its applications into various industries, including pharmaceuticals, electronics, and food packaging. One of the most notable developments has been in the realm of automation. Companies are now increasingly incorporating robotic systems that enhance the precision and efficiency of micro dispensing processes. These automated systems allow for high-throughput dispensing, reducing the time taken to complete tasks and minimizing human error, thereby improving overall productivity.
Furthermore, the integration of advanced software solutions has revolutionized micro dispensing systems. These software tools enable real-time monitoring and control of dispensing operations, providing operators with valuable insights into process performance. With features such as predictive maintenance, users can identify potential issues before they lead to breakdowns, thereby enhancing reliability. Moreover, software advancements facilitate seamless connectivity with other manufacturing systems, leading to greater synchronization across the production line. The combined effect of automation and smart software is paving the way for more streamlined and efficient workflows.
Another area of innovation is the development of smart dispensing solutions that utilize Internet of Things (IoT) technology. These systems can collect data from the dispensing process, allowing for better analytics and feedback loops. By utilizing this data, businesses can optimize their dispensing strategies, leading to reduced waste and improved product quality. For instance, real-time data can help calibate dispensing parameters, ensuring that precise amounts are used in applications that require meticulous measurements.
In light of these advancements, it is clear that the future of micro dispensing is leaning towards increasingly intelligent systems that not only enhance efficiency but also adapt to dynamic production environments. As industries continue to embrace these innovations, we can expect further improvements in workflow and an expansion of micro dispensing applications across various sectors.
Challenges in Micro Dispensing
Micro dispensing technology, while offering numerous advantages across various industries, is not without its set of challenges. One of the primary technical limitations stems from the intricate nature of dispensing at such reduced volumes. Engineers often encounter issues related to precision and accuracy, requiring advanced equipment and mechanisms to ensure that the right amount of material is dispensed consistently. The tolerance levels in micro dispensing applications are significantly tighter compared to standard dispensing procedures, which necessitates meticulous calibration and potentially complex setup processes that could hinder production efficiency.
Another prominent challenge relates to material handling. Many substances utilized in micro dispensing, particularly adhesives and other viscous materials, can exhibit difficulties in flow characteristics at reduced volumes. The tendency for clogging, air bubbles, or inconsistent flow can disrupt the dispensing process, leading to waste and unpredictable results. Handling particulate-laden materials, such as those containing nanoparticles or fillers, poses additional complications, demanding specialized equipment and techniques to maintain material integrity and performance during the dispensing operation.
Cost factors also play a critical role in the widespread adoption of micro dispensing technologies. The initial investment in high-precision dispensing equipment can be substantial, and companies must weigh these costs against anticipated productivity gains. Moreover, while micro dispensing can enhance efficiency in certain applications, the savings generated must be sufficient to justify the investment in both equipment and skilled personnel capable of operating and maintaining such technology. To mitigate these challenges, companies are increasingly engaging in collaborative efforts with suppliers to develop customized solutions tailored to specific operational needs, ensuring a more efficient approach to micro dispensing processes.
The Future of Micro Dispensing Technologies
Micro dispensing technologies have gained significant traction across various industries, including pharmaceuticals, biotechnology, electronics, and cosmetics. As we look towards the future of these innovations, several emerging trends are positioning micro dispensing as a critical component in both product development and manufacturing processes.
One of the leading trends is the integration of automation and robotics within micro dispensing systems. Automation is expected to enhance precision, reduce labor costs, and streamline production processes. As companies seek to increase efficiency while maintaining quality, we are likely to see more sophisticated automated micro dispensing solutions, capable of handling high volumes with minimal human intervention. This shift will be particularly crucial in medical and pharmaceutical applications, where accuracy and consistency are paramount.
Another driving force behind the evolution of micro dispensing technologies is the increasing demand for personalized products. Industries such as skincare and pharmaceuticals are beginning to tailor solutions based on individual customer needs, leading to a greater reliance on micro dispensing methods. This customization trend will encourage system manufacturers to develop more versatile dispensing technologies that can adapt to different formulations and product specifications on-the-fly.
Market growth in key sectors is further expected to boost research and development in micro dispensing methods. As businesses recognize the cost-effective benefits of micro dispensing, investment will likely increase, resulting in more innovative applications. Additionally, as technology advances, we can anticipate enhanced accuracy and the ability to dispense increasingly complex fluids or materials. This will not only expand the scope of micro dispensing but also improve its reliability across diverse fields.
As we contemplate the future of micro dispensing technologies, it is essential to recognize the vast opportunities that lie ahead. Companies willing to embrace these innovations may find themselves at the forefront of their respective industries, driving advancements that could shape the next generation of products and services.
China
Liandong Yougu Garden, No.1 East Second District, Jiansha Road, Danzao Town, Nanhai District, Foshan City
TENSA TECHNOLOGY (Subsidiary of FST Dispensing pump)
Email : sales@tensatech.com
Singapore
12 Joo Koon Crescent #01 Singapore 629013
Tel : +86 13360343644
Whatsapp : +86 13360343644